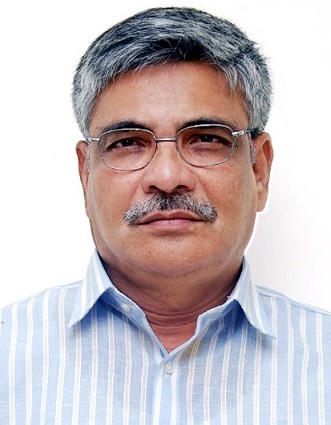
Dr. Venugopal Srinivasan
Present Designation:
Senior Consultant, Auroville Foundation, An Autonomous Institution under Ministry of Education, Government of IndiaAreas of Interest:
Rolling, Forging, Extrusion, Sheet Metal Working, Constitutive Modelling, Robotics and Automation, In-service Inspection, Friction and wear.
Specialisation:
Metal forming, Tribology, Materials Development, In-Sodium Testing, Robotics and Automation, Inservice Inspection
Major Professional Contributions:
Major Contributions:
1. In Research and Development:
• 36 years research experience in the area of Metal Working. Published about 100 journal papers, 30 publications in proceedings and submitted three theses. Guided 25 B.Tech., projects, 20 M.Tech., 5 Ph.D., Theses. One Book is in Print and the other Book in advance stage of completion.
• Setting up of facilities for metal forming studies at IGCAR, which includes installation, commissioning and operation of 2Hi/4Hi Rolling mill of capacity of 200 ton roll separating force. Pneumatic forge hammer of 250 Kg tup capacity, Triple action hydraulic press of 250 ton capacity, Mechanical press of 63 ton capacity, Swaging machine, Vacuum melting and casting plant, vacuum heat treatment furnace and wire drawing machine of 2 ton capacity. Designed and built high strain rate high temperature Compression Testing Machine.
• Executed of the project on “Facilities for Materials Testing in Flowing Sodium up to 600oC. (INSOT).” Designer of all the critical components for high temperature service in flowing sodium, such as heat exchangers, cold traps, dump tanks, expansion tanks, economizers, level indicators, flow meters, test chambers for creep and fatigue testing, special machines and piping layout and supports for the above facility.
• Involved in the indigenous development of large size plates of 8000 mm long X 2000 mm wide X 30 mm thick stainless steel type AISI 316LN, Modified 9Cr-1Mo and A48P2 carbon steel plates in collaboration with Rourkela Steel Plant, Rourkela, Steel Authority of India.
2. In Product Development:
Designed and fabricated the following equipment:
a. Undertaken the development of In-Service Inspection Vehicle (Robot) for the inspection of main and safety vessels of Proto-Type Fast Breeder Reactor.
b. Undertaken the development of mobile inspection vehicle for the inspection of storage tanks of a chemical plant.
c. High temperature high vacuum tribometer capable of working up to 800oC and at the vacuum level of 3X10-7 torr.
d. Hot torsion testing machine for workability testing and simulation of hot rolling and forging processes
e. High temperature silicon carbide split furnace to test materials up to 1300oC
f. Residual stress measurement X-ray camera
g. Creep machines of 3 ton capacity to test materials up to 850oC
h. Fixtures for impact testing of radioactive materials
i. Chambers and loading system for conducting Creep and Fatigue testing in flowing sodium
j. Hydrogen permeation cell for diffusion measurements
k. Testing facility for CERT and Fracture toughness tests under in-situ hydrogen charging
l. Solar Wax Melter, Solar Milk Heater, Solar pump and Bio-gas plant (during student days).
3. Significant Research Activities:
3.1. Established the optimum processing windows for hot, warm and cold working of stainless steels type AISI 304L, 316L, 316LN, and 304 and Modified 9Cr-1Mo steel, using dynamic materials modelling technique. Processing maps have been generated for the above materials in the cold, warm and hot working regions. The usefulness of these maps for controlling the industrial processes such as press forging, extrusion and hammer forging, has been proved through detailed experimental investigations carried out at actual industrial process conditions. Application of this work has resulted in lower rejection rates (less than 2 %) and higher yields in the production of nuclear grade stainless steel tubes.
3.2. Developed a novel strategy for optimising microstructural changes during hot deformation using control theory principles. This work is the first known application of systems engineering principles for optimising microstructure development during hot working processes. This method has been applied to the optimisation of grain size development and certain process parameters such as die geometry and ram velocity during extrusion of plain carbon steel and stainless steel type AISI 304L. It has been proved beyond doubt that this method ensures higher productivity with consistent quality of the products.
3.3. Some of the major contributions in the area of bulk forming are: (i) Determined the optimum processing conditions for enhanced deformation response of intermetallics (-TiAl and composite materials, (ii) Transferred advanced materials processing technology to copper extrusion industries for improved tool life, surface quality, uniformity of material flow for hot tube-extrusion of high-phosphorous copper to a reduction ratio of 1:116, (iii) Investigated the hot deformation behaviour of a new class of ultra-light weight structurally porous Ti-6Al-4V. Evaluated the constitutive flow behaviour of this new material (a system consisting of gas + solid) and recommended an innovative design approach for processing this material without increase in the product density and inherent blistering problems. (iv) Investigated and solved the stress induced porosity problem during cogging operation of large Ti-6Al-4V sections, which bothered aircraft industries over the years, (v) Developed a new process for the manufacture of -TiAl automobile exhaust valves through isothermal extrusion and (vi) Developed new strategies for monitoring metal forging operations using acoustic emission technique. The above contributions have far-reaching scientific and technological applications.
3.4. Collaborative Work: The following are the major collaborative research projects handled by me as Principal Investigator/Collaborator:
i. Development of indigenous technology for the manufacture of special materials for the construction of Proto-type Fast Breeder Reactor in collaboration with Steel Authority of India Ltd. The total cost of which is about USD 0.5 million.
ii. Development of Technology for Teflon coating of 8000 mm dia 300 mm thick bearing support rings of Proto-type Fast Breeder Reactor in collaboration with M/S AMI Polymers, Ankleshwer. The total cost of which is about USD 0.25 million.
iii. Development of miniature bellows for In-Sodium applications in collaboration with M/S Metallic Bellows, Chennai.
iv. Development of Plasma assisted Aluminising of Inconel strips, Plasma Nitriding on Stainless Steels and Plasma assisted Teflon coating on metals and elastomers in collaboration with Institute of Plasma Research, Ahmadabad.
v. Development of Technology for manufacturing Porous metallic tails by Casting in collaboration with PSG College of Technology, Coimbatore.
vi. Development of various Robotic devices in collaboration with IIT, Kanpur, Central Metal Forming Research Institute, Durghapur and other Industries.
vii. Investigations on the tribological behavior of hard facings on stainless steels in collaboration with Indian Institute of Technology , Madras, Indian Institute of Science, Bangalore, Indian Institute of Technology, Delhi and Welding Research Institute, Trichy.
4. No. of Ph.D. guided:
4.1. “A Study on the Influence of Weld Parameters on Performance of Centrifugal Extractor used in Fast Reactor Fuel Reprocessing,” Shri A. Ravishankar Homi Bhabha National Institute (HBNI)
4.2. Study of Pulsed Laser Seamk Welding and Pulsed Laser-GTA Hybrid Welding on AISI 316 Stainless Steel Shri A. Masilamani Chelladurai Homi Bhabha National Institute (HBNI)
4.3. Modeling and Analysis of Transient Thermal Responses during Dissimilar Welding of 316L Stainless Steel and Mild Steel using Pulsed ND:YAG Laser Shri K. Sureshkumar University of Madras
4.4. Comparison of Weld Characteristics of Axisymmetrical and Non-Axisymmetrical Butt Weld Pipe Joints Shri Satish Kumar Velaga Homi Bhabha National Institute (HBNI)
4.5. Design and Development of Out-of-pile Version of Instrumented Capsule for Online Determination of Uniaxial Creep Behavior in Structural Specimen Shri Sadhu Venkatesu Homi Bhabha National Institute (HBNI)
5. In Teaching:
• Director of National Institute of Technology Nagaland and Teaching and guiding research in the area of Metal Forming and Metalurgy.
• Visiting Professor in IIT Madras for teaching and guiding research in the area of Metal Forming.
• Adjunct faculty in Homi Bhabha National Institute, Mumbai and guiding Ph.D., M.Tech., Thesis in the area of Metallurgy and Robotics,
• Serving as one of the Board of Governors in the Governing Board of National Institute of Technology Puducherry, Karaikal.
• Serving as Member, Academic Council, Pondicherry Engineering College, Puducherry.
• Serving as Member, Board of Studies for Department of Mechanical Engineering, SRM Institute of Technology (Deemed University), Kattankolathur, Tamil Nadu.
• Serving as Member, Board of Studies for Department of Mechanical Engineering, Annamalai University, Annamalai Nagar, Tamil Nadu.
• During the period of M.S. Programme at IIT Madras, assisted professors in teaching assignments in the following capacities:
i. B.Tech., Mechanical: Teaching and demonstration on Metal
Forming Machines - two and half years
ii. HAL Management Trainees: Laboratory assignments - two and half years
iii. M/S TVS Sundaram Fasteners: Five weeks short term course - Tutorial Assignments.
• In Indira Gandhi Centre for Atomic Research, Kalpakkam taught courses on “Furnace Technology”, “Metal Forming Processes” and “Strength of Materials” to the Trainees during 1983-‘84.
• Guest faculty in Department of Metallurgical Engineering, Indian Institute of Technology Madras, during July - December 1998 and July 1999 –December 2000 and offered course on Theory of Plasticity and delivered a lectures in the area of Advanced Metal Forming Processes to M.Tech., Students and guided two M.Tech., Thesis with Prof. P. Venugopal.
• Evaluated large numbers of Ph.D., Thesis of IISc., Bangalore, IIT Madras, Bharathiyar University, Tiruchirappali and Anna University and a few M.S., Thesis of IIT Madras, Chennai, Regional Engineering College, Tiruchirappalli.
• Served as Member, Board of Studies for Department of Metallurgical Engineering, PSG College of Engineering and Technology, Coimbatore and Department of Production Engineering, Annamalai University, Annamalai Nagar.
• Served as a Member, Academic Council, Anna University.
• Served as Executive Committee Member, Centre for Industrial Consultancy and Sponsored Research, Anna University, Chennai.
6. Patent:
• “Optimization and Control of Microstructure Development During Hot Metal Working”, a joint invention of James C Malas, W. Garth Frazier, Enrique A. Medina, Venkat Seetharaman, S. Venugopal, R. Dennis Irwin, W.M. Mullins, S.C. Medeiros, Anil Choudhary and Raghavan Srinivasan, US Air Force Patent No. 6,233,500 dated May 15, 2001.
Consultancy Areas:
Metal Forming, In-service Inspection of Nuclear Reactors, Infrastructure Projects of Higher Education
Sector Associated With:
Educational and Research Institutions, Nuclear Industries
Sectors Interested to Offer Service:
Educational and Research Institutions
Professional Experience
45 years
Keywords
Metal Forming, Rolling, Forging, Extrusion, In-service Inspection, Automation, Higher Education
Education
B.E., M.S., Ph.D., D.Sc.
Awards and Recognitions
Awards & Honours received:
1. Recipient of TVS Charities Scholarship for my PUC and B.E., Courses (i.e., from the year 1972-73 to 1977-78).
2. National Research Development Corporation (NRDC) of India Student Invention Talent Contest Award for the gadget “Solar Wax Melter”, in the year 1978.
3. NRDC of India Student Invention Essay Contest Award for the essay on “Solar Pumping Plant”, in the year 1977.
4. Karaikudi Tamil Sangam Essay Competition Award for the Essay on “Welding of Metals”, in the year 1977.
5. I.T. Mirchandani Memorial Award of Indian Institute of Welding for the research paper on “Electro-slag Welding of AISI Type 316 Stainless Steel” for the year 1989.
6. Best Paper Award for the paper presented in the National Seminar on Advances in Metal Cutting and Metal Forming Organised by Anna University held at Madras on May 24-25, 1990.
7. United States National Research Council - United States Air Force Office of Scientific Research Resident Research Associateship Award, Washington, USA, 1995.
8. “Metallurgist of the Year –2001” award of the Indian Institute of Metals for the outstanding contributions in basic research, applied research and technology transfer in the area of Deformation Processing of Austenitic Stainless Steels.
9. “Best paper award” for the paper titled "ISI Systems for Fast Reactor Fuel Reprocessing Plants – A Collective Panorama" - V. Rakesh, C. Rajagopalan, Saji Jacob George, S. Venugopal and K.V. Kasiviswanathan presented at the INAE-DAE International Conference on Advances in Manufacturing Technology (ICAMT 2008) for Young Engineers February 6-8, 2008, IIT Madras, Chennai.
10. “SAIL Gold Medal” of Indian Institute of Metal for the research paper on “An FEM Based Methodology for the Design of Dies for Near-Net-Shape Manufacturing of Petals for Fabrication of Multiple Curvature Large Size Vessels of Fast Breeder Reactor Project” by Utpal Borah, Shreedhar Venugopal, R. Nagarajan, P. V. Sivaprasad and S. Venugopal, published in Transactions of the Indian Institute of Metals, Vol. 60, No. 5, October 2007, pp 1-20.
11. Elected as a Life Fellow of the Indian Institute of Metals (FIIM).
12. Elected as a Fellow of Indian National Academy of Engineering (FNAE).
13. Member, Academic Council, Anna University.
14. Member, Research Advisory Council, Jawharlal Nehru Aluminium Research, Design and Development Centre, Nagpur, Ministry of Mines, Government of India.
15. Editor of Journal of Manufacturing Engineering, Transactions of the Society for Manufacturing Engineers (India).
16. Elected as a Fellow of the American Institute of Materials International (FASM).
17. Appointed by MHRD, Government of India as one of the Board of Governors in National Institute of Technology Puducherry, Karaikal.
18. Member, Academic Council, Pondicherry Engineering College, Government of Puducherry,
19. Elected as the Fellow of Academy of Sciences (FASc.), Chennai in the year 2014.
20. Recipient of “Life Time Achievement Award,” from Lions Club International District 324AL and Lions Club of Pudupattinam in 2015.
INAE Section Affiliated
VIII: Mining, Metallurgical and Materials Engineering
Year of Election to Fellowship
2006
Year of Birth
1955
Disclaimer
(i) INAE is not responsible for any activity/interactions that results from the contact with the Expert.
(ii) Information in individual Expert page has been provided by the Expert himself/herself and INAE is not responsible for the information provided